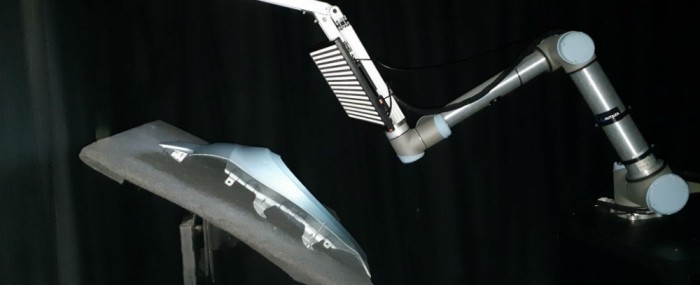
The automotive industry uses artificial intelligence in vehicle inspection
02 de outubro de 2018By Claudia Izique | FAPESP Research for Innovation – Autaza Tecnologia began its development at the Aeronautical Technology Institute’s Manufacturing Competency Center (CCM-ITA) located in São José dos Campos, São Paulo State, Brazil. Founded in 2016, Autaza is opening an office in Detroit, Michigan (USA), and has global customers in the automotive and aerospace industries. Its revenue doubles every year.
“Our goal is to be the leader in Brazil and a benchmark for smart quality inspection in the US and Germany by 2022,” says Renan Padovani, one of the founders of the startup, which is supported by FAPESP’s Innovative Research in Small Business Program (PIPE).
The story of this firm began with a research and development project that brought together ITA and General Motors (GM) in São Caetano do Sul, São Paulo State, and resulted in a functional prototype of a system that uses computer vision and artificial intelligence (AI) to detect defects on the surface of car bodies. The new technology is an alternative to the visual inspection method currently used by most auto makers, which requires human inspectors trained to identify and classify defects.
The automated quality inspection system’s positive results and GM’s willingness to permit use of its intellectual property in the new system motivated the three researchers responsible for the project at ITA to found the firm and bring the technology to market. “GM itself adopted the project while it was still embryonic and tested the technology on its production line,” Padovani recalls.
Six months after the technology was tested in São Caetano do Sul, GM also implemented it in the US and at the German plant where it then produced the Opel. This unit was sold in 2017 to Peugeot and BNP Paribas but is still a customer of Autaza.
While the three founders were developing the first prototype for GM, they saw an opportunity to use AI to detect defects in paint and coatings on other kinds of substrate, such as composites used by the aircraft industry. “This opened up a new market and brought customers as large as Embraer,” Padovani says.
Mathematical model
In the inspection system developed by Autaza, a special wall of light projects a zebra pattern on the object. A camera captures the reflected black-and-white fringes of light on the surface of the car or aircraft. The images are analyzed by software to identify and classify defects in terms of 12 mathematical parameters. “The system ensures car or aircraft body quality and facilitates communication with correction teams,” Padovani says.
In addition to being more efficient than visual inspection, the mathematics-based technology used by Autaza’s system is also an improvement on traditional automated inspection models, according to Padovani. “Traditional inspection systems require data from CAD [computer-aided design] files and vehicle geometry, among other information, so that they can detect flaws by comparison. Our mathematical model is developed in advance and already contains data on the defect, accelerating the inspection process,” he explains.
The system also saves a great deal of time in the preparatory phase. It takes approximately six months to prepare an inspection template that looks for defects by comparing the product with an ideal standard. With Autaza’s pre-established mathematical model, it takes only a fortnight. “The AI already knows what the defect is,” Padovani says.
Robot cell
Not much more than a year after its inception but after it had won GM’s custom, Autaza was selected for PIPE Stage 1 funding, which calls for proof of concept. The aim was to upgrade the algorithm used to classify car body defects. Padovani acknowledges that in light of the advanced stage already reached by the project, he could have applied for Stage 2, which calls for prototype development. “However, the funding from FAPESP helped us structure our technical planning, and we gained industrial maturity,” he says.
In September 2018, the firm won approval for another project from the PIPE/PAPPE Grant Program, also known as PIPE Stage 3. This project called for industrial and commercial development of the system. The PIPE/PAPPE Grant Program resulted from an agreement between FAPESP and the Brazilian Innovation Agency (FINEP), a federal government body. “We’re creating the first Brazilian 3D scanner 3D for defect detection and implementing robotics in our inspection system,” Padovani explains.
With FAPESP’s support, the firm plans to buy high-performance computers that will shorten the time taken to inspect a car body and enhance its competitiveness compared with traditional systems, which inspect a car on the assembly line every minute. “The aim is to reduce automatic inspection time to 45 seconds, from two minutes currently,” he says.
This improvement will be made possible by the introduction of a robot cell into the inspection process. It will be tested at Autaza and then installed at GM. “The robots won’t be the conventional kind. They’ll be collaborative robots that interact with human workers. That’s the concept at the heart of industry 4.0,” Padovani notes.
Company: Autaza
Site: www.autaza.com
Address: Parque Tecnológico de São José dos Campos, Avenida Dr. Altino Bondensan, 500 - Bloco Cecompi, São José dos Campos (SP), CEP 12247-016, Brazil
Tel: +55 12 3876-7757