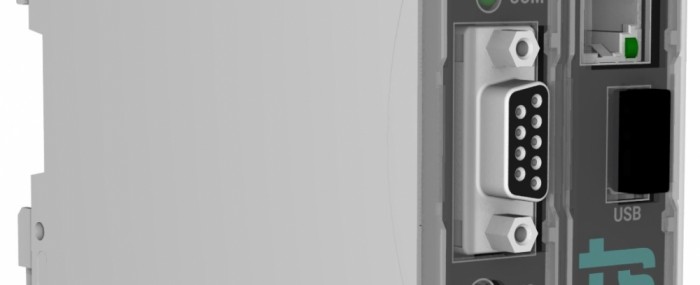
System based on Brazilian technology monitors industrial networks
09 de janeiro de 2024By Roseli Andrion | FAPESP Innovative R&D – When it was founded in 2011 in São Carlos, São Paulo state, Brazil, Toledo e Souza Engenharia (TS) began by selling on the domestic market a German solution for monitoring industrial networks. Some time later, the German company that produced the solution was taken over by another firm, and the distribution agreement ceased to be worthwhile for TS. Adverse commercial conditions, in conjunction with lack of technical support, motivated engineers at TS to create a product with Brazilian technology for the same purpose.
The decision enabled TS to offer this type of monitoring to local customers without depending on third parties, via a platform that permitted standardization across various manufacturers, guaranteed high data rates, and was cost-effective in terms of installation and maintenance.
Monitoring of such networks is essential to anticipate failures and control operating costs, furnishing the information required for preventive maintenance and repair, and generating data that helps managers with planning, integration and oversight of operations.
The type of network technology involved here is known as Profibus (short for process field bus), a widely used industrial communication protocol in automation and process control systems. It connects and exchanges data between field devices such as sensors, actuators, and higher-level control systems.
TS now offers Profibus monitors and analyzers that use data from the network to predict and correct failures, helping to reduce the stress and damage caused by unplanned downtime in a factory. They also save on the cost and time taken by maintenance. The technology is entirely indigenous and support is provided in Portuguese.
Development of the platform began in 2017 with support from FAPESP via its Innovative Research in Small Business Program (PIPE). The project was successful in that the product had the basic prerequisites and a degree of stability, but it was not commercially viable. “The researcher responsible for the code left the firm, and the product still had many limitations,” says Paulo Toledo, an electrical engineer and co-founder of TS.
He decided to take a new team on board and develop the solution differently. “We changed the platform and programming language,” he recalls, adding that for various reasons the new version was funded in-house. “We needed to create something more quickly.”
The functions remained the same, but the design and development were entirely reformulated. “It was a really great project, but it isn’t the system we have now. We were obliged to develop yet another solution. During the project conducted with funding from PIPE, we learned above all which pathways not to follow,” he explains.
The process was an intense learning experience for the team. “The corrections that came later, and the product we launched after that, have a lot of what we learned on this journey,” he says.
Changing concept
Initially, Toledo continues, the product was to be a gateway for information that would stay with the customer, where a supervisor would receive data, but the concept was changed and the product restructured. “The system is now 100% embedded and uses technology that is fully Industry 4.0 capable,” he says, adding that the solution works with every kind of supervisory or data processing system, such as Power BI, an enterprise business intelligence platform.
Embedding the solution in the factory rather than storing data in the cloud, which could have been cheaper, ensures that connection failures do not lead to significant data losses. “Intranet downtime, for example, doesn’t affect the flow of data, which is entirely local, so that nothing is lost,” he says. This is the main advantage of the current system. “The information can be used in a great many ways. Some customers with large projects send the data to Power BI, for example. This final model is effective and efficient.”
Although the team knew storing data locally was the best option, the initial decision to create a system with a supervisor had to do with the skills and competencies of the researcher responsible for developing the solution. “He was in charge of design and development at the time. Only he knew the language, so he made that choice,” Toledo recalls, noting that this may have been a significant mistake. “It entailed inflexibility and affected the product’s future.”
Extensive product line
TS has extended its product line since development of the monitoring solution began. It now has 14 products covering the entire range of network protocols. “In recent years, we’ve invested heavily in development. The system begun with PIPE funding was to have been our first product, but changes had to be made, and we ended up launching another solution based on network analysis software first,” Toledo says.
TS’s Profibus network monitoring system can be implemented along with two complementary solutions. TS Profibus Monitor keeps tabs on data exchanges across the entire network, with the capacity for 5,000 events in its registration log, while TS Scope DP monitors the physical medium of a Profibus DP segment, and TS Scope PA supervises the physical medium of two to four Profibus PA segments.
TS invested BRL 450,000 (about USD 90,000) of its own funds in development in 2023. “We plan to invest more than BRL 1 million in the next two to three years,” Toledo says.
Among other things, this will include upgrading the existing network monitor. “We currently use a commercially available motherboard. I want to make all our hardware totally industrial and proprietary, which requires substantial investment,” he says.
TS is the only firm in Latin America that offers Profibus network analysis and monitoring solutions, as it has been since its foundation in 2011, according to Toledo. Its customers are in the sugar and ethanol, automotive, pulp and paper, mining and chemical industries.