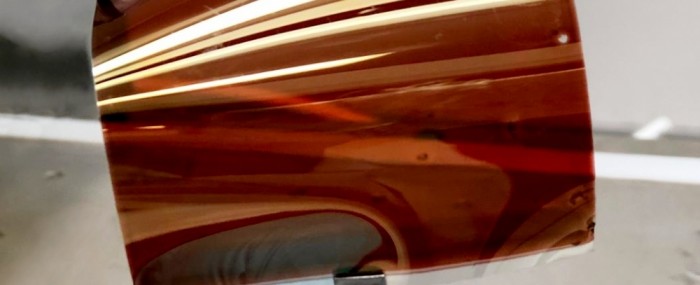
Startup achieves success with machine that produces thin films from soluble materials with many applications
16 de janeiro de 2024FAPESP Innovative R&D – Researchers at Autocoat, a startup hosted by the State University of Campinas’s tech incubator (INCAMP) in São Paulo state, Brazil, have developed a machine that produces laboratory-scale thin films from soluble materials with potential applications in several research fields. Examples include film with suitable properties for perovskite photovoltaic solar cells, biomaterials for wound dressing and tissue regeneration, and novel drug and cosmetic delivery systems.
The thin film deposition machine was designed as part of a project supported by FAPESP via its Innovative Research in Small Business Program (PIPE). It uses a technique known as blade coating, in which multiple layers of material in solvents are deposited on a rigid or flexible substrate and the blade spreads the solution evenly over the substrate to form a thin film.
BCC-02, as the device is called, can produce films as thin as 10 nanometers (nm) and as thick as tens of micrometers. A nanometer is a millionth of a millimeter. A micrometer, or micron (μm), is a thousandth of a millimeter. “The quality is similar to that obtained by spin coating,” says Viviane Nogueira Hamanaka (https://bv.fapesp.br/en/pesquisador/17180/viviane-nogueira-hamanaka), a chemist with a PhD in electrical engineering, and a founding partner of the startup.
Spin coating, which is widely used in research, development and industrial processes to produce thin film, involves depositing a material in solution on the center of a glass slide or other smooth substrate as it spins at high speed so that the centrifugal force spreads the solution over the surface to form a thin film. “The problem is that too much of the material spins off the substrate altogether and is wasted,” Hamanaka says. “It’s also hard to reproduce exactly the right shape of film by industrial-scale spin coating.”
According to her, the BCC-02 is more efficient, using up to 20 times less soluble material and making fuller use of it to produce thin films, most of which measure 7 cm x 7 cm (or less). “The films produced by our machine also exhibit excellent uniformity and a high degree of reproducibility,” she says.
Academic origins
Autocoat was born in 2020 while Hamanaka was researching for her PhD in electrical engineering at the University of São Paulo’s Engineering School (POLI-USP). “I was working on methods of producing organic light-emitting diodes [OLEDS], used in digital displays for TVs, smartphones, computers and so on,” she recalls.
These materials are typically fabricated by physical vapor deposition of small organic molecules, a process with a high capital cost and a slow rate of deposition.
“I suggested to my thesis advisor, electrical engineer Fernando Josepetti Fonseca, that blade coating would be a better method. He agreed, as long as I succeeded in developing an automated production system,” she says.
Two months after they started the firm, Hamanaka and her business partner were awarded funding for a PIPE phase 1 project, which enabled them to develop the first prototypes to demonstrate the BCC-02’s technical and scientific feasibility. In early 2022, they won approval for a PIPE phase 2 project, which enabled them to optimize parts of the system in preparation for commercialization in Brazil and abroad.
The optimized parts were mainly the controls that regulate the temperature of the substrate for the soluble material and adjust the blade’s position and speed. The machine now produces uniform film with low roughness, comparable to those produced by spin coating, regardless of thickness.
They also used the funding from PIPE to equip the machine with a nitrogen air knife for low-temperature film drying and perovskite crystallization. This enables the BCC-02 to produce films with suitable properties for the fabrication of perovskite solar cells, whose high performance and low cost make them highly promising for the renewable energy market.
Because they are flexible and light, perovskite solar cells can be used to generate electricity from sunlight in objects such as curtains, backpacks and vehicle roofs, extending the possible applications of photovoltaic technology. “Our device is the only one on the market with this nitrogen air knife,” Hamanaka says.
There are many potential applications. “In laboratories, the BCC-02 can be used to make films from biomaterials for wound dressing and tissue regeneration, as well as novel drug and cosmetic delivery systems,” she says.
They first planned to complete development of the machine in 2023 and then launch it commercially. “However, many researchers to whom we showed the products asked if they could buy the prototypes right away, so we decided on an earlier launch date,” she recalls. “We prepared to pitch it at the XX Brazil MRS Meeting organized by the Brazilian Materials Research Society and held in Foz do Iguaçu in September 2022.”
The choice was strategic. “We knew the meeting offered an opportunity to present the technology to a large number of Brazilian and foreign researchers in several areas of materials research,” she says.
Interest and acceptance surpassed expectations, possibly because the product is easy to operate and competitively priced. Another advantage is that it can be used by scientists in different fields and by laboratories of all sizes. “We came back from the event with several orders. Since then we’ve sold ten units of the BCC-02,” she says.
The machine has also been noticed by large corporations, including the German multinational MBRAUN, one of the main producers of gloveboxes – hermetically sealed containers with gloves built into the sides to enable scientists to handle sensitive materials in a controlled environment. “The BCC-02 is small enough to be used in the inert atmosphere of a glovebox,” she says.
The partnership with MBRAUN has recently been strengthened by approval of a PIPE phase 3 project for development of a more robust business plan. Although the BCC-02 has already been launched, the firm is using the funding to make adjustments and optimize the device for use in glovebox systems. If all goes well, MBRAUN will buy the BCC-02 and integrate it into the gloveboxes it sells to labs around the world.