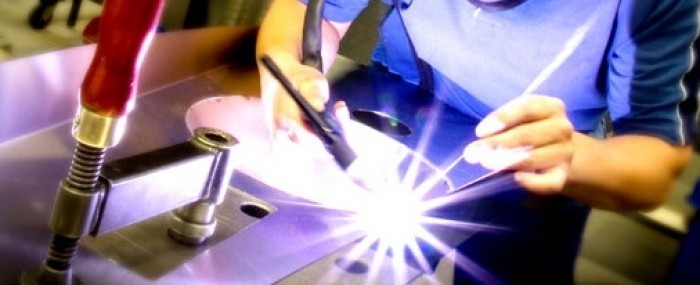
Laser machining services for industry and R&D for medical and dental sector
01 de agosto de 2017Lasertools was founded in 1998 to offer manufacturers expertise in the use of lasers to the Energy and Nuclear Research Institute (IPEN) in Brazil. "No one then knew about laser cutting, and it was a huge success," recalls physicist Spero Penha Morato, one of the seven founding partners.
At the time, Morato had retired from IPEN, where he was CEO between 1990 and 1995, and had just returned home after serving as a United Nations consultant on industrial laser applications, and as he recalls, this led to the idea of setting up a company.
The idea prospered thanks to a fertile environment: the University of São Paulo (USP), which hosts IPEN had just opened a Center for Innovation, Entrepreneurship & Technology (CIETEC) in partnership with IPEN. This was the first tech startup incubator in São Paulo.
A year earlier, in 1997, the São Paulo Research Foundation (FAPESP) had launched its Innovative Research in Small Business (PIPE) program. Lasertools was approved in PIPE's first call for proposals, in which the first seven startups to be incubated at CIETEC were selected. Its project "Applications of Lasers in Materials Processing" was accepted in PIPE's third call.
The company's original aim was to act as a job shop providing laser machining services for such materials as steel, titanium, silicon and ceramics, among others, to add value to the activities of the manufacturing industry. "The product portfolio ranged from dental drills and implants to molecular sieves, with a great deal in between," Morato says.
In two years, Lasertools expanded. "We were one of the first startups to graduate from CIETEC. We set up shop in the Rio Pequeno neighborhood near USP," Morato recalls. At the time, the company developed solutions for the automotive, medical and dental, machine and metalworking, appliance, and gift industries.
It used a solid-state neodymium-doped YAG laser for industrial cutting, drilling and welding. With support from PIPE, it extended use of the technology to increase levels of power and peak capacity as well as processing speed, and made micromachining more feasible.
In 2002 Lasertools won FAPESP's approval for a bolder project to develop laser manufacturing methods and processes for biocompatible metal implants, including coronary and peripheral stents. "This was incremental rather than radical innovation," Morato says.
A stent is a small tube of metal mesh inserted with a balloon into a heart artery or peripheral blood vessel that has become blocked by plaques of fat or calcium. The necessary laser-cutting technology and stent prototypes were developed by Lasertools, which also evaluated the implant procedures in partnership with the Heart Institute (InCor) at USP's general and teaching hospital, Hospital das Clínicas. "We had to find partners when the project matured and required additional expertise that wasn't part of our profile as a job shop," Morato says.
Stent production involves coating with drugs to prevent future blockage of the blood vessel. This required a new solution, so Morato and partners set up a new firm called Innovatech Medical. Also with support from PIPE, the new firm embarked on the development of laser-processed stents. The end product, Cronus, is sold by Scitech Medical, based in Goiânia, Goiás State.
"Once we had everything up and running, I sold my share in Innovatech to the partners in Goiânia, and we transferred the technology to them. I went back to working under contract and remained exclusively with the job shop at Lasertools," Morato says.
"We're now working on the development of an aortic valve replacement," he adds. This is also a bioprosthesis and is used in the treatment of aortic stenosis and heart failure due to aortic valve calcification.
The project received funding from PIPE between 2013 and 2015, during which period Lasertools became equipped to perform precision laser cutting of metal alloy sheets and tubes suitable for production of this bioprosthesis. The main innovation was the replacement of the previously used technology, which involved wire erosion cutting, with faster and more precise laser cutting of flat sheets.
"In parallel with this research and development, we remained loyal to our mission of acting as a job shop, meeting demand from industry and even engraving gifts," Morato says. The latter is performed by LaserTools Promocional, a spinoff with facilities in the vicinity of Rua 25 de Março in São Paulo. "We've managed to put lasers into everything," he concludes.
###
Also published at Eurekelert: www.eurekalert.org/pub_releases/2017-08/fda-lms083017.php