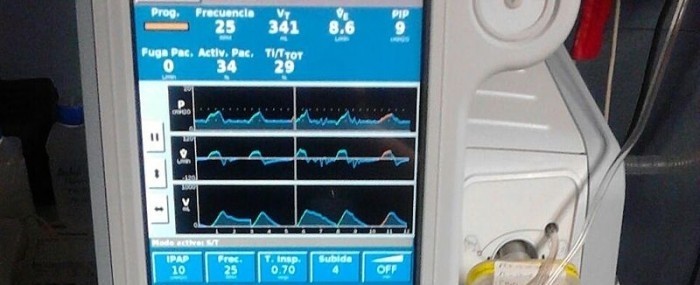
Brazilian firm refines mechanical ventilation technology
02 de junho de 2020By Eduardo Geraque | FAPESP Innovative R&D – The COVID-19 pandemic has triggered a worldwide race to develop efficient, low-cost mechanical ventilators for the treatment of critically ill patients.
When they evaluated ten projects to develop new ventilators, however, the team of researchers at Setup Automação e Controle de Processos, a company based in Campinas, in the state of São Paulo, Brazil, found that most were not sufficiently robust to be used continuously for the two weeks required by such patients on average. Moreover, the equipment did not comply with the minimum criteria for the control of vital functions in critical patients.
“The developers of these ventilators invested in projects that produced low-cost but not very efficient equipment or machines with complex technology that’s hard to operate,” engineer William Robert Heinrich, one of the company’s partners, told FAPESP Innovative R&D.
To offer solutions without these technological limitations, the company is developing a project that it expects to lead to two new models of portable ventilators.
The project is supported by FAPESP’s Innovative Research in Small Business (PIPE) Program. It was one of the first six projects selected in a call for proposals issued by PIPE in partnership with FINEP, the Brazilian government’s innovation agency, to fast-track funding for anti-pandemic products, services or processes developed by tech startups and small businesses in the state of São Paulo.
“We plan to have prototypes for both ventilators ready within three months,” Heinrich said.
One of the portable ventilators will be designed for use in field hospitals, and the other will be designed for use in intensive care units (ICUs).
The main difference between the two is their functionality. Ventilators used in regular hospital wards and field hospitals are simpler. They basically keep the patient alive by supplying oxygen to the lungs. In ICUs, they have to be more robust and are typically much more expensive, so a more affordable model would be welcome.
“Ventilators for ICUs have to be capable of monitoring the patient’s vitals, as well as controlling oxygen flux, delivery and volume. They help medical staff diagnose the patient’s condition and choose the right treatment,” Heinrich explained.
The firm plans to develop ventilators that are easy to operate and can be used in places remote from large urban centers. “We have plenty of experience in all areas of engineering involved in building a ventilator,” Heinrich said.
Indeed, Setup has a 24-year track record in industrial automation, where it has consistently innovated in areas such as pneumatics, mechanics, hydraulics, and closed-loop control. As part of the project, it is currently developing an automated test station for the calibration of ventilators of all kinds.
“Calibration typically takes between four and eight hours. We want to cut that to minutes,” Heinrich said.
Technological adaptations
The researchers aim to produce ventilators on a commercial scale in under seven months, offering them to both private and public hospitals.
To speed up development and surmount obstacles such as a shortage of ventilator components on the market, the firm is partnering with as many other Brazilian manufacturers as possible to produce import substitutes.
For example, the plan is to repurpose the injector nozzles mass-produced in Brazil for flexible fuel automotive vehicles at an affordable cost.
“The automotive industry already requires suppliers to produce these components in clean rooms, an even more important requirement in the case of ventilator components,” Heinrich said.
The devices will be adaptable for use in complex surgeries on animals performed by vets, he added. “Adaptation for use with small or large animals will be very straightforward,” he said.